P:REACT
The future of PET recycling
The PET recycling machine P:REACT makes it possible to revolutionize the PET recycling process. It transforms PET waste and PET bottle flakes into food-grade recycled PET in minutes.
Description
Thanks to the advanced LSP (Liquid State Polycondensation) process, the PET melt phase is used to trigger the polycondensation of PET. The reaction speed in the PET melt is significantly higher than in the solid phase. The clear advantage: IV values, controlled with pinpoint accuracy, that can be even higher than those of the original starting material – depending entirely on your objectives.
Additionally, we have paid attention to highest energy efficiency and minimization of operating costs when developing the PET recycling machine P:REACT – profitability is thus guaranteed.
At a glance
- PET recycling at the highest level
- Output rate up to 3.000 kg/h (6,600 lbs/h) depending on type
- Continuous process with enormous process stability
- Significantly higher energy efficiency than conventional SSP applications
- Approval by FDA and EFSA for 100 % food safety
In addition, NGR provides all the equipment for conveying pellets such as blower, pipes, cyclones and much more.
Technology
The liquid state polycondensation process (LSP)
The LSP-Process utilizes the inherent capability of PET to condensate in the molten phase under vacuum. This condensation leads to an increase of IV. The high performance vacuum effectively decontaminates the material from harmful chemicals, – securing further use of the material for 100% food contact.
As molten PET enters the vertical part of P:REACT, strands are formed to create a suitable surface to volume ratio. The material is then collected in a horizontal drum and slowly pushed forward. Condensation starts immediately as the strands are formed and is set forth until PET exits P:REACT. IV increase is controlled by the residue time and the vacuum level of the molten PET inside P:REACT and therefore can be adjusted to a desired level. The settings of parameters allow the control unit to maintain the desired IV-level within a small tolerance-band.
The decontamination performance is extremely effective, as carried out in the liquid phase of PET. The cleaning of the material exceeds limits set by recognized food safety standards, but also effectively removes spin oil from fibers.
Continuous operation by design
The continuous operation of P:REACT provides rPellets within a narrow IV-range, suitable for usage in valuable high end applications (i.e. fiber-spinning or sheet extrusion). Batch related IV-fluctuations are simply designed out.
Rapid IV-increase
The favorable conditions inside P:REACT (temperature/ surface:volume ratio of the melt/high performance vacuum), easily initiates the condensation-process of PET. This results in IV increase rates of some 0.01 dl/g per minute. Faster reaction leads to faster results and a more profitable operation.
Automatic control of IV-level
P:REACT actively controls the residue-time of the PET-melt and the vacuum inside the reactor and automatically adjusts the machine parameters to receive the desired IV at a consistent level.
High decontamination performance
The separation of harmful contaminants, as spin-oils or those components not desired for food contact, are removed by high performance vacuum. This high decontamination performance allows the use of P:REACT for many applications for highest flexibility.
FDA and EFSA approved for 100% food contact
The European Food Safety Authority (EFSA) and the U.S. Food and Drug Administration (FDA) both confirm that the Liquid State Polycondensation (LSP) process is fully food-safe.
High energy efficiency
The recycling of PET requires the material to be melted. P:REACT uses the melt-energy for condensing PET. The reactor itself only maintains the heat-level. P:REACT is therefore highly energy-efficient, which results in low operating costs.
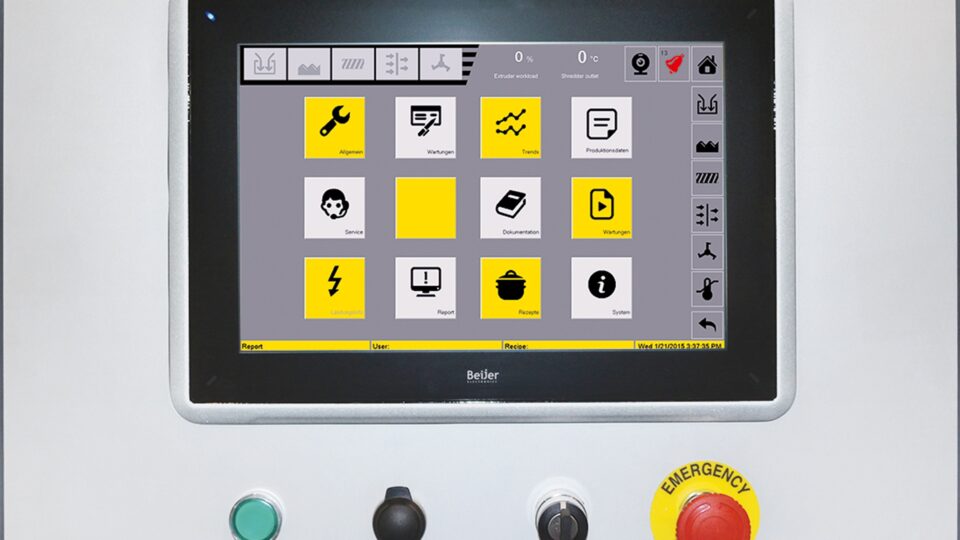
Central control unit
Central control unit
All equipment functions of P:REACT and the recycling-equipment (melt preparation unit) are controlled via the central terminal. Recipes are managed with this easy to read and write NGR touchscreen, thereby securing traceability as well as reproducibility.
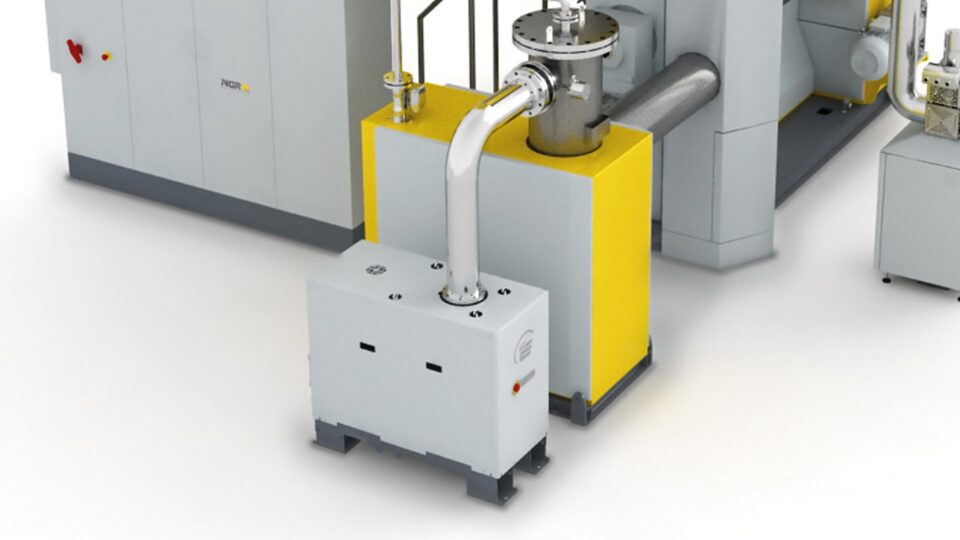
Vacuum unit
Vacuum unit
For initiating the polycondensation of PET and to effectively remove non-desired chemicals, the P:REACT is permanently kept under vacuum. The gases received from the LSP-Process undergo treatment in the condensation unit.
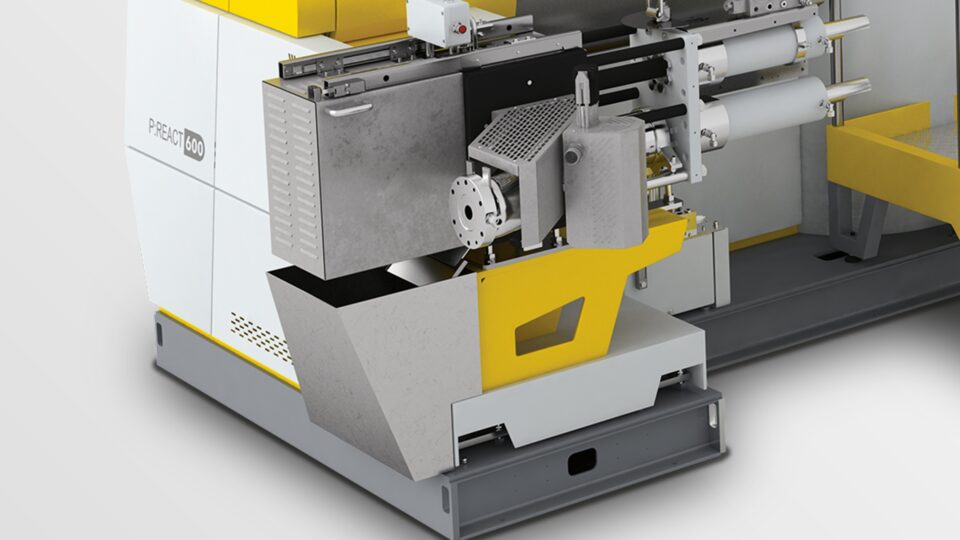
Continuous IV measurement
Continuous inline IV measurements
At the end of P:REACT, the IV-value is continuously and automatically measured. This measurement is the basis for adjusting the automatic system controls for achieving most consistent IV rates in the rPellet resp. finished product. The IV measurements are stored in the central control unit and are used for traceability, thereby actively supporting quality-management.
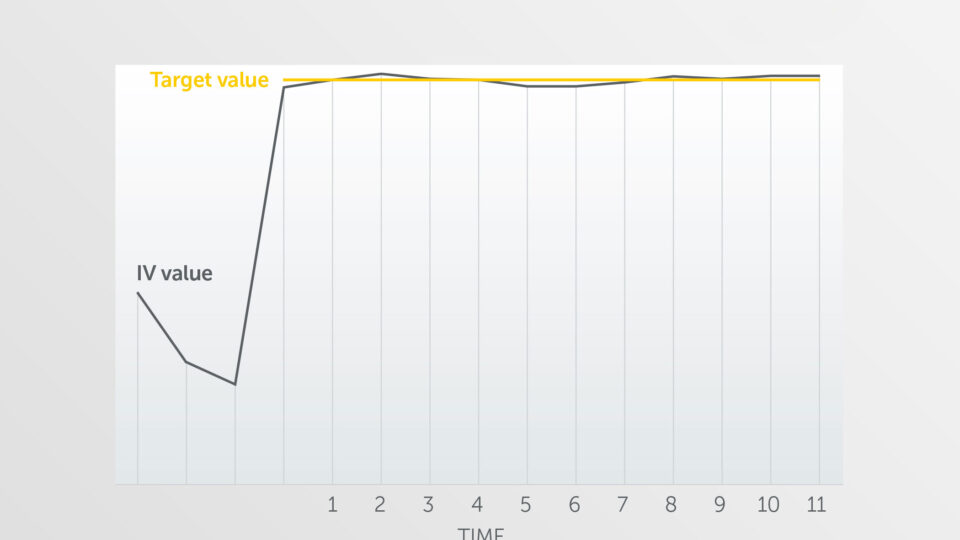
Typical IV-structure
Controllable IV-structure
Due to the conditions prevalent in the melt reactor, ethylene glycol is removed. The equilibrium of the melt shifts in favor of higher degrees of polymerization. This process results in a chainlink generation of PET and subsequently in an increase of the intrinsic viscosity (IV) depending on the residence time of the melt in the vacuum container and the intensity of the vacuum. Thus, the IV value can be controlled actively using these two parameters. Deviations from the desired value are always kept within a minimum tolerance.
Typical IV curve: IV-decrease during plasticizing and subsequent increase up to the target value. The IV value is kept within a narrow tolerance band during decontamination.
Exceeding the highest expectations for production
Connecting to a film production system
Significantly increased production volume and minimized process downtimes at the same time – the advantages of the P:REACT and its enormous process stability are plain to see. The more uniform material thickness of the films in downstream production, made possible by the process stability, reduces production costs – as does the option of modifying conventional formulations and of reducing the often fed virgin PET material or to cut it out completely. Thus, the use of the P:REACT becomes an important contribution to efficiency and practiced sustainability.
Starting materials
Some of them are: Loose film, reject rolls, edge trims, start-up lumps, punch scrap, reject parts, post-consumer PET (bottle flakes, trays, etc.)
A real bonus
- Changes of color are possible at any time in running operation – in contrast to other systems, shutting down and cleaning the machine to change color is a matter of the past with the P:REACT.
Connecting to a fiber production system
Fiber production is known for its stringent requirements for the recycling process. Here, P:REACT can take full advantage of its enormous process stability and push the output rate up to a previously unknown level. Minimized downtime increase the production volume significantly. Additionally, the effective decontamination during the melt phase results in reliable removal of chemical agents such as spinning oils. In short: P:REACT is the perfect partner for your reliable and stable fiber production.
Starting materials
Some of them are: Fibers, fabric, fleece (nonwovens), textiles, post-consumer PET (bottle flakes, trays, etc.)
A real bonus
- The unique process stability of P:REACT reduces fiber breaks and thus enables significantly increased product quality.
- Reliable decontamination.
Connecting to a production system for straps
A high and stable IV value is the basis for the production of high-quality straps. Here, the P:REACT demonstrates its strength in the exact control of the desired IV values. The improved quality, simultaneously combined with a reduction of the production costs (by reducing or omitting the addition of virgin PET material) renders the P:REACT the winner in the cost-benefit calculation.
Starting materials
Production waste, post-consumer PET (bottle flakes, trays, etc.)
A real bonus
- The IV increase up to the desired target value is the condition for a better product that can also sell at a higher price.
Production of PET pellets
The effective decontamination and the precisely controllable IV buildup turn the P:REACT also into the ideal technology for the production of recycled pellets (rPET pellets), usually upstream of the flexible distribution on different production lines for further processing. There is one special feature that makes P:REACT score highly: consistent quality output despite feeding the most varied production and post-consumer waste.
Starting materials
Practically all common starting materials can be used, some of which are loose film, reject rolls, fabrics, production waste, post-consumer PET (bottle flakes, trays, etc.)
A real bonus
- The IV increase up to the desired target value is the condition for a better product that can also sell at a higher price.
- The decontamination right in the melt phase is highly effective and improves the degree of purity of the finished rPET enormously.
Add-Ons
Pelletizing
Filter
Test equipment
Pelletizing
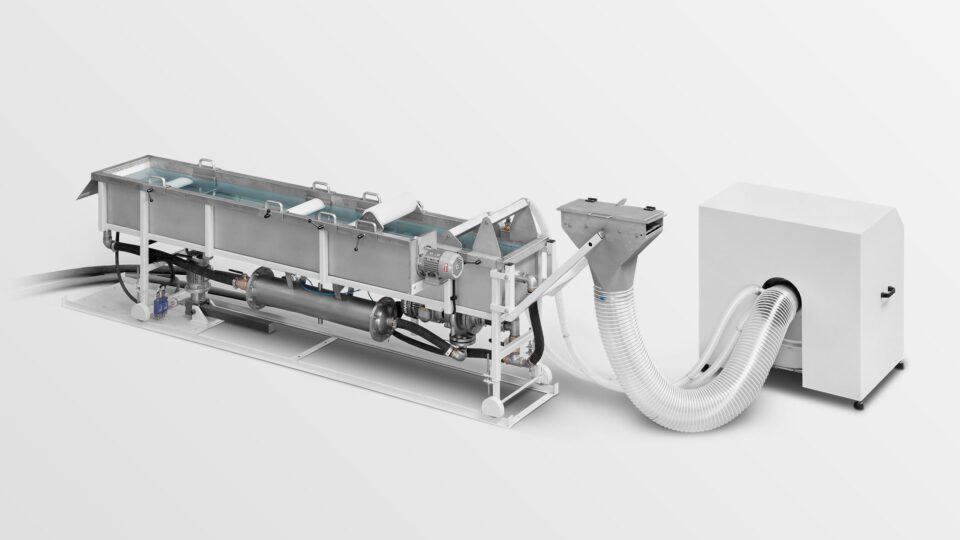
Strand pelletizer
Strand pelletizer (SP)
For low-viscosity melts. The melt emerges from strand nozzles, is cooled in a water bath, dried by means of a fan and cut to the desired length in the pelletizer. The result is cylindrical, dust-free pellets with excellent mixing properties.
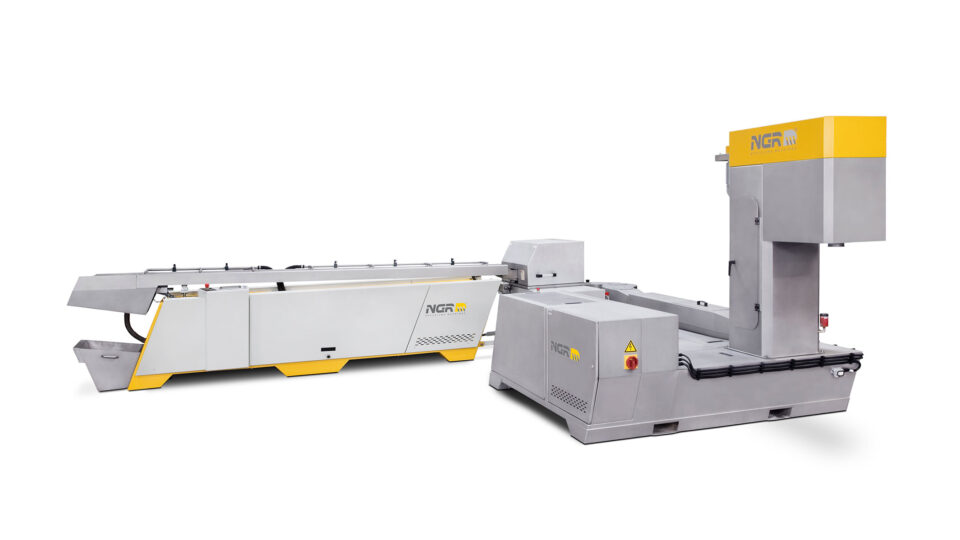
Automatic strand pelletizer
Automatic strand pelletizer (A-SP)
In addition to the benefits of the SP, the A-SP option offers the added convenience of fully automated start-up. The strands are transported automatically by a water slide to the pelletizer, and the pellets are dried in a centrifuge.
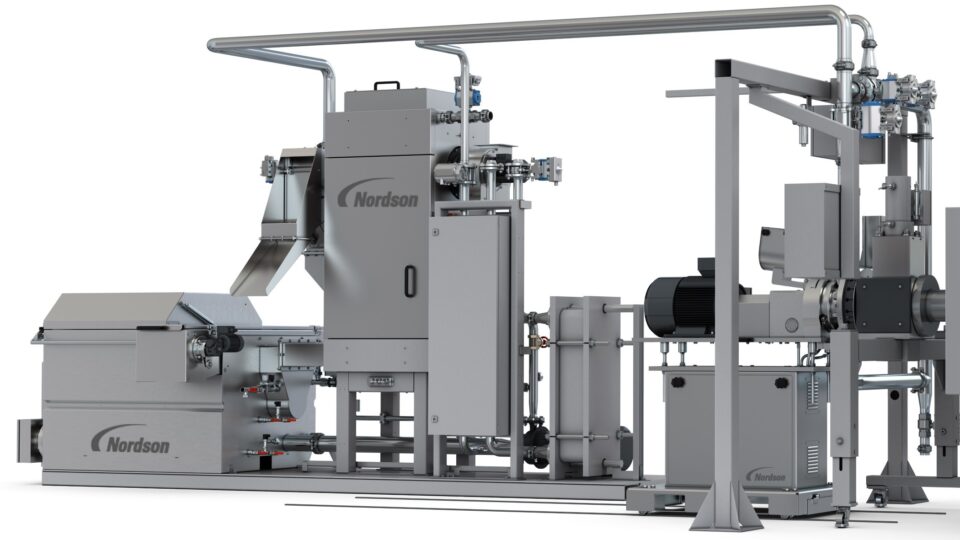
Under Water Pelletizer
Underwater pelletizer (UWP)
For difficult-to-process (e.g. sticky) polymers or thermoplastics with a very high melt flow index. The melt emerges from the die plate and is knocked off by the pelletizer blades. The whole process takes place under water. In the centrifuge, the pellets are separated from the process water and dried.
Filter

Backflush screen changer
Back-flush screen changer
For heavily contaminated materials. The hydraulically operated double-piston screen changer filters the melt in a process-controlled and continuous manner. The integrated backwash device automatically cleans the screens. The number of back-flushes and the related service life of the screens depend on the degree of contamination of the material.

4K Backflush screen changer
4K back-flush filtration
For heavily contaminated materials. In contrast to the standard backflush screen changer with 2 screen cavities, this system is equipped with 4 screen cavities. The double filtration surface with the same frame size results in a longer filter life.
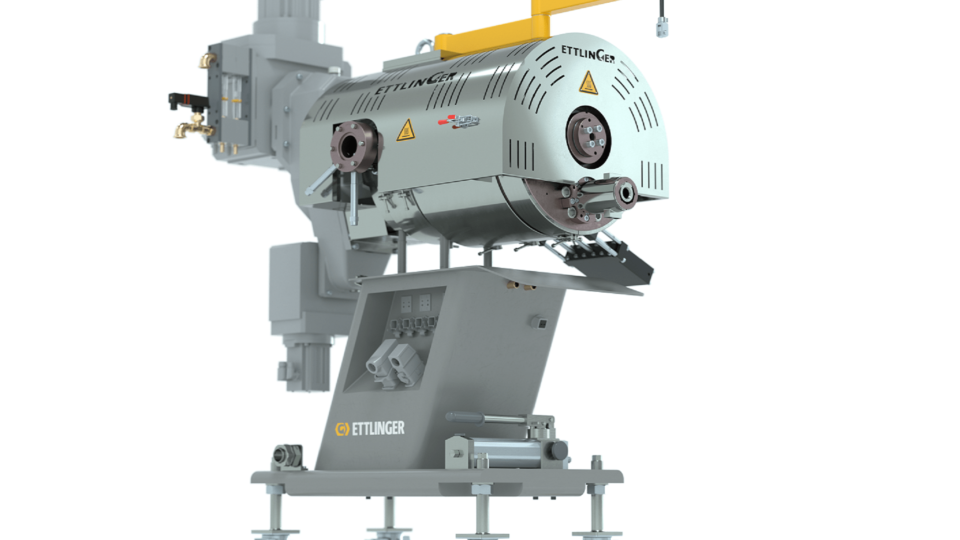
High-performance melt filter
High-performance melt filter
The continuous melt filters in the ERF series are suitable for a wide range of moderate and highly contaminated polymers and provides a pressure constant operation, long screen lifes, very low melt losses and a compact design. By the permanently rotating filter drum foreign particles are being constantly and effectively removed, depending on the application ERF melt filters enables throughputs from 150 to 10,000 kg/h.
Test equipment
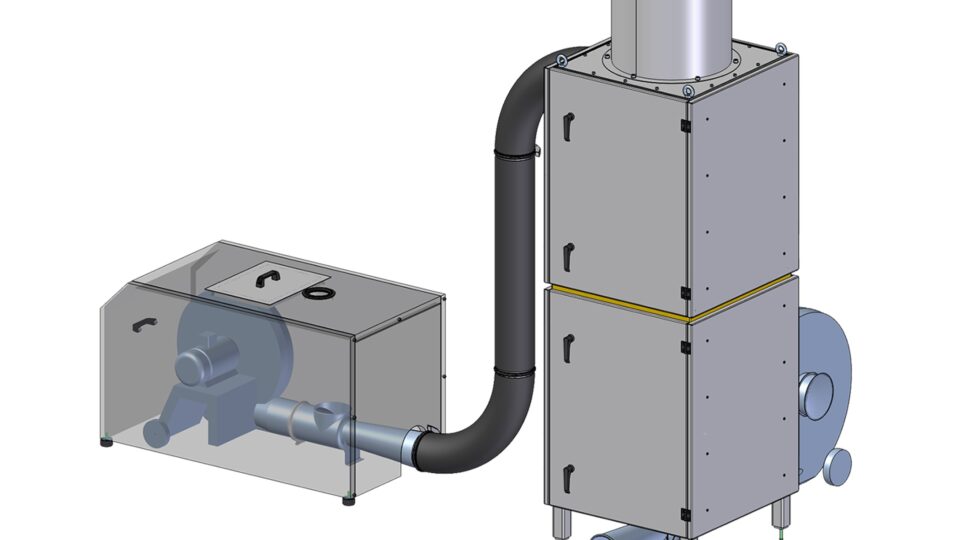
Flow scale
Flow scale
The throughput scale is integrated in the machine control system and displays the current production output in kg/h (lbs/hr). The data can be logged in a BDE system.
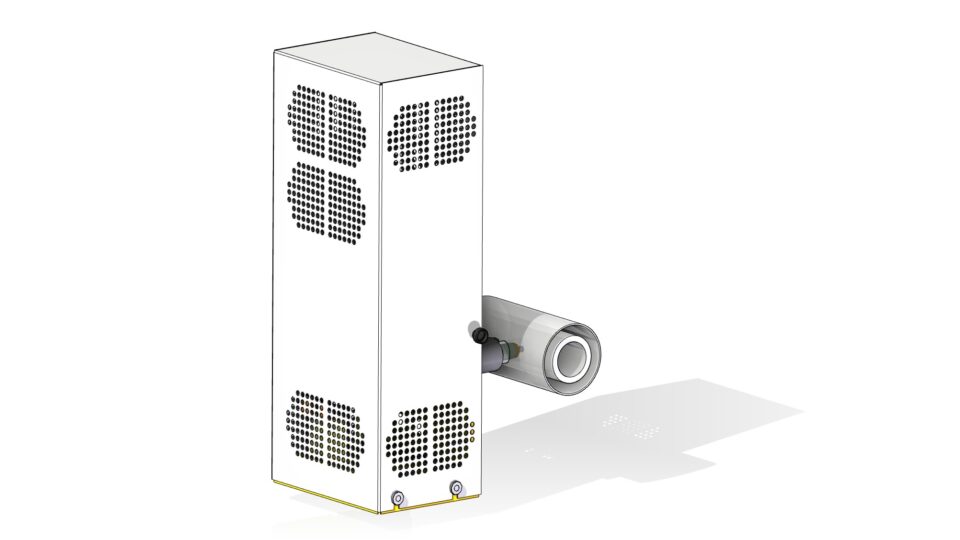
Online viskosimeter
Online Viscometer
For continuous melt viscosity measurement. Melt is taken from the production extruder, the viscosity is measured, and then the melt is returned to the extruder.
Based on the differential pressure across the capillary, the viscosity of the material (IV value, MVR) is determined by means of a stored recipe.
Material samples
Support
Our all-round service – satisfaction included
Excellent technology calls for excellent service. Our 100% commitment to flawless service ensures maximal cost efficiency and minimal downtime.
Our services
- Service hubs for the fastest possible processing of all maintenance and repair work
- Spare parts centers for flexible responses to strong markets
- High spare parts availability thanks to particularly high stock levels in Europe and North America
- Worldwide extruder screw production for short-term production or repairs
- Starter and spare parts packages for every new machine
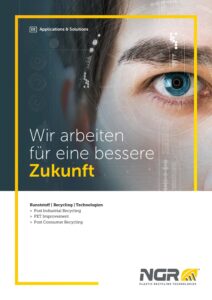
NGR Applications & Solutions
[5 MB]
Petras-H: A new hope
All hope was shattered.
All dreams were gone.
UNTIL NOW…
Watch the movie to see how the Liquid State Polycondensation (LSP) process brings back hope for Petras-H.