Filter
Depending on the application, a variety of filter systems is used. The melt is cleaned efficiently with low melt loss. Basically, the appropriate filter is selected in consultation with the customer. Depending on the degree of contamination, the following variants are available as standard.
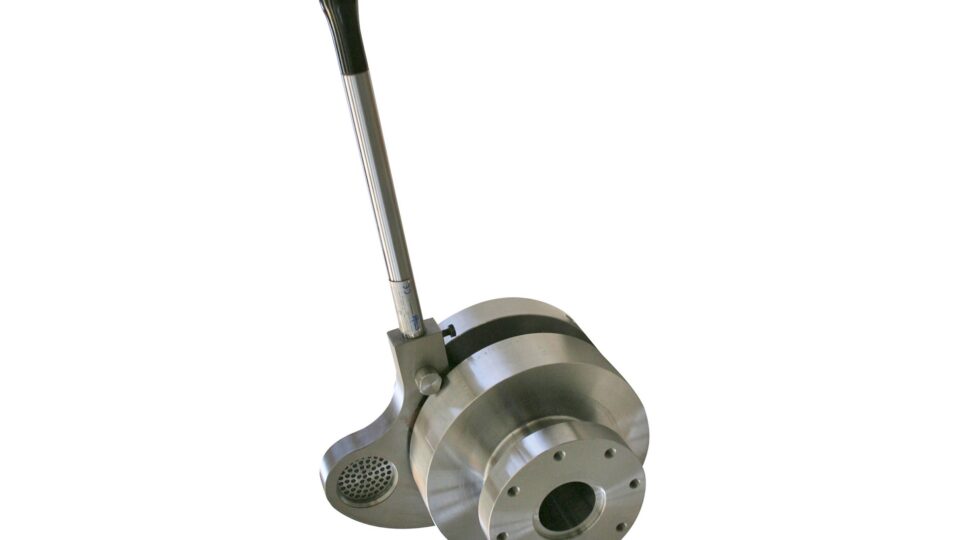
Manual screen changer
For clean, in-house production waste. Using the manual lever, two screens can be swung out alternately to allow for cleaning of the melt stream. The process is discontinuous, because the machine has to be switched off to change the screen.
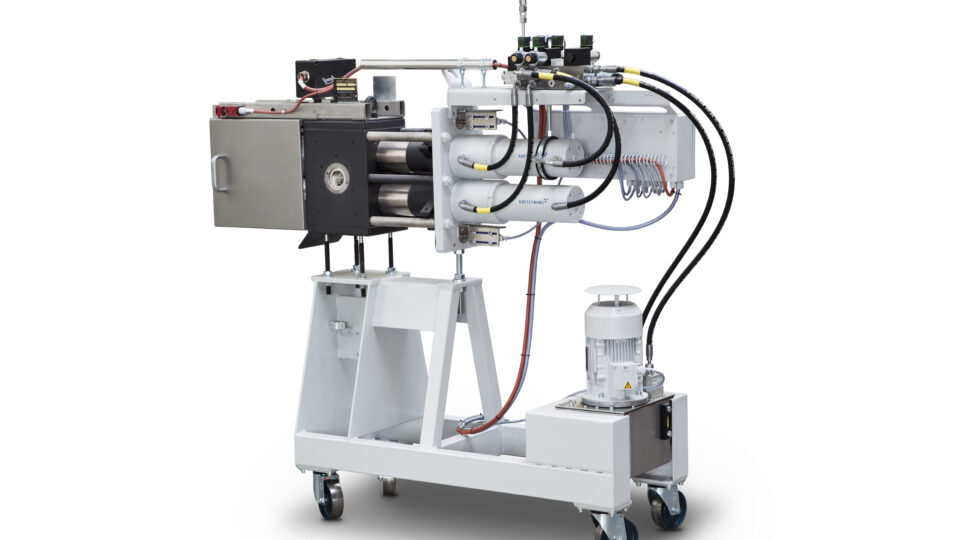
Double-piston screen changer
For light impurities. The hydraulically operated double-piston screen changer allows continuous filtration of the melt. This allows a screen change without process shutdown.

Back-flush screen changer
For heavily contaminated materials. The hydraulically operated double-piston screen changer filters the melt in a process-controlled and continuous manner. The integrated backwash device automatically cleans the screens. The number of back-flushes and the related service life of the screens depend on the degree of contamination of the material.

4K back-flush filtration
For heavily contaminated materials. In contrast to the standard backflush screen changer with 2 screen cavities, this system is equipped with 4 screen cavities. The double filtration surface with the same frame size results in a longer filter life.
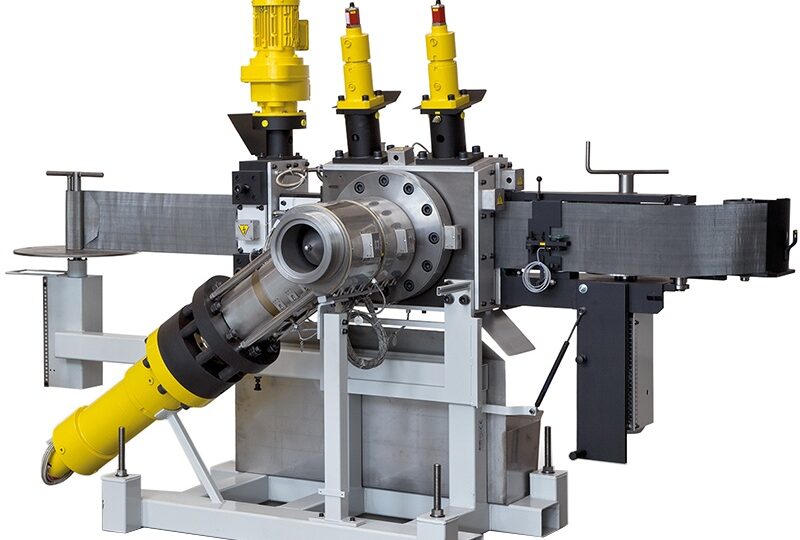
Band melt filter
For high contamination at high throughput rates. With the lowest melt losses and low filter costs, fully automatic operation ensures excellent filtration results. It is used particularly for post-consumer plastics.
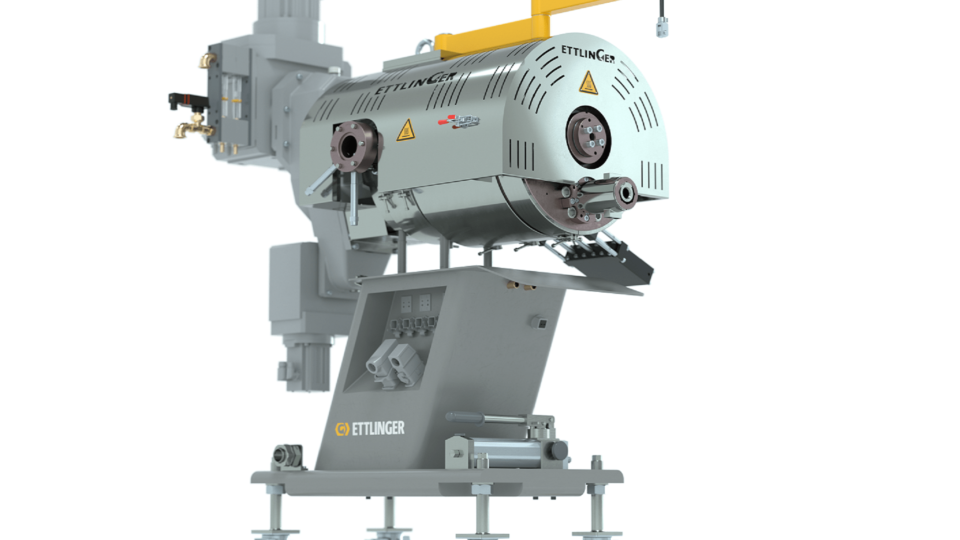
High-performance melt filter
The continuous melt filters in the ERF series are suitable for a wide range of moderate and highly contaminated polymers and provides a pressure constant operation, long screen lifes, very low melt losses and a compact design. By the permanently rotating filter drum foreign particles are being constantly and effectively removed, depending on the application ERF melt filters enables throughputs from 150 to 10,000 kg/h.