S:GRAN
The evolution of the market leader
The S:GRAN is the latest development in our successful shredder-feeder-extruder combination, with over 1,200 patented installations worldwide since continuous production began in 1997.
Description
S:GRAN is the perfect solution for processing scrap plastic materials of a variety of types, materials and shapes created by industrial processes. Even thick-walled scrap plastic materials as well as fibers and textiles can be processed without additional pre-shredding.
The plastic recycling technology of S:GRAN meets even the highest standards for efficiency and achieves zero- waste production (all production waste is fed back in) thanks to shredding that conserves an outstanding amount of material as well as optimally guided extrusion.
At a glance
- Simple, high quality processing of post industrial waste of any type
- An evolution of our patented single-shaft shredder/extruder combination.
- Throughput rates up to 900kg/h
- minimal operator interaction, one button, easy start-up and shut-down
- NXT design platform, flexible, modular construction with multiple options
- Faster ROI, and lower OpEx with the latest generation technology
* Output values for LDPE according to NGR company standard, depending on material and quality.
In addition, NGR provides all the equipment for conveying pellets such as blower, pipes, cyclones and much more.
Technology
The operating principle of S:GRAN
Plastic waste is processed by a heavy duty shredder operating at low speed for gentle size reduction and minimal loss of material properties. in this process, a hydraulic ram pushes the material into the shredder drum.
The shredder and extruder drives are controlled separately and automatically, based on load.
After shredding, the material is fed directly into the extruder. in the extruder, the material is brought to a uniform melt temperature and degassed, if necessary.
All the components are positioned in close proximity to prevent oxidation of the material and to make optimal use of heat from the shredding process.
This patented combination of shredder, feeder and extruder is a feature of all units in the S:GRAN line.
One-step-technology
In a single process step, the slow-turning shredder blades grind up the plastic waste and the shredded material is then fed continuously to the extruder.
Process bulky plastic scrap
Large, thick or bulky waste can be processed without pre-shredding as long as pieces fit into the hopper opening.
One-button automatic ON/OFF control
The control system provides for smooth start-up of equipment components. Restart after unplanned shutdown in less than two minutes with full hopper and full extruder.
Dump and run operation
The material level in the hopper is constantly measured and the feed is regulated accordingly. Discontinuous filling of the conveyor is possible – the NGR control unit does the rest.
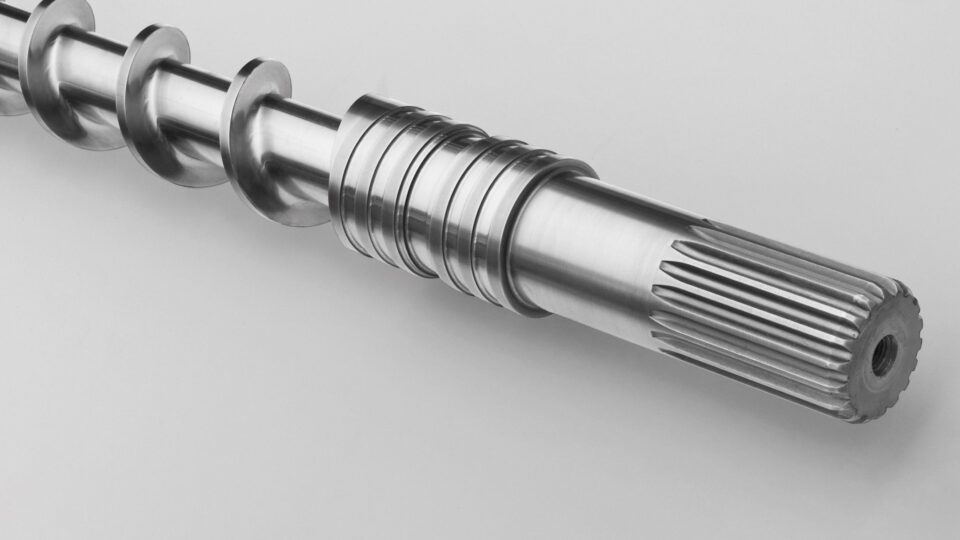
Extruder screw
Extruder screw
Specially developed for the challenges of recycling, the universal extruder screws provide optimum melt homogeneity and process material efficiently with minimal loss of physical properties. For special requirements, our expert NGR engineers develop custom-tailored screw geometries.
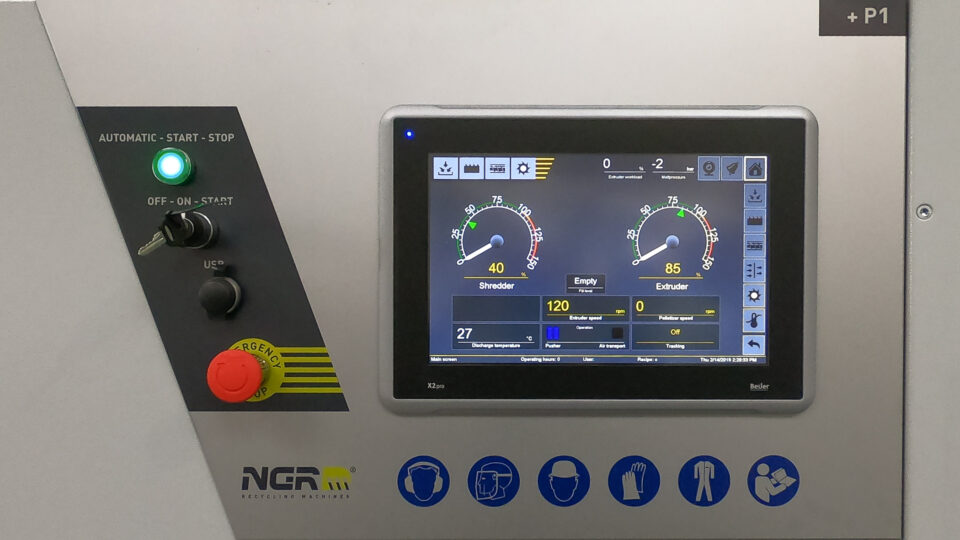
Control unit
Control unit
All equipment functions from feeding to pelletizing are controlled automatically from the easy-to-read NGR touchscreen. Recipes are managed in the operator control unit, which increases traceability, provides ease of use, and ensures equipment parameters are set properly.
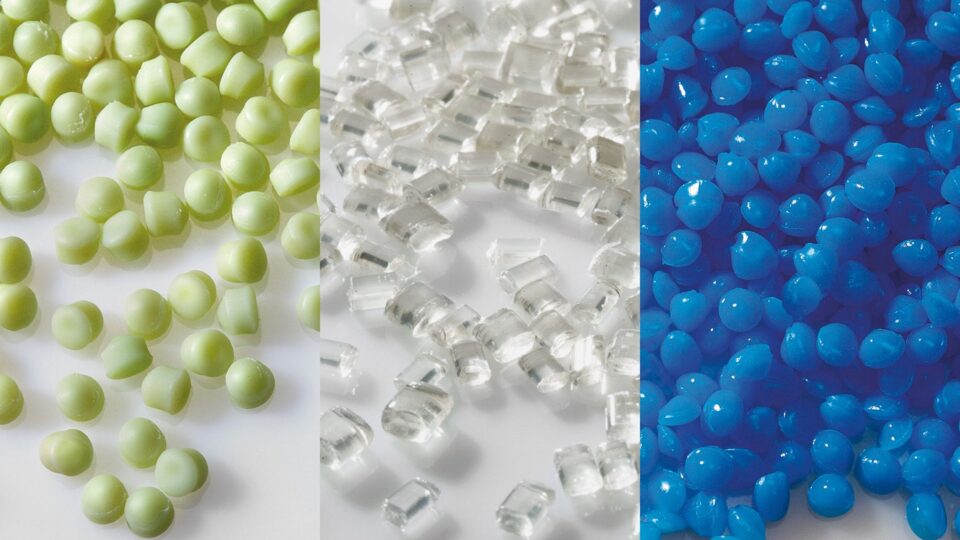
High-quality pellets
Pellet size
In addition to high quality, the uniform pellet size also provides for homogeneous mixture in new material. NGR thus plays an indirect role in ensuring consistent quality in the final product.
Add-Ons
Feed-in
Degassing
Pelletization
Filter
Peripherals
Test equipment
Feed-in
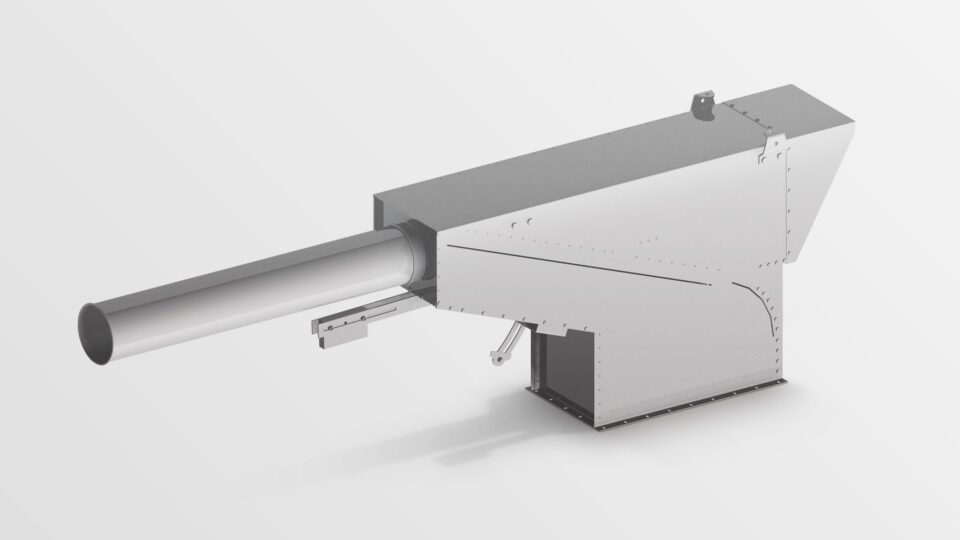
Air separator
Air Seperator
The air separator is used in the production process to continuously recycle film edge trim, which is fed pneumatically into the machine. With “inline operation,” further material handling is unnecessary, and the NGR recycling machine is now fully automated.
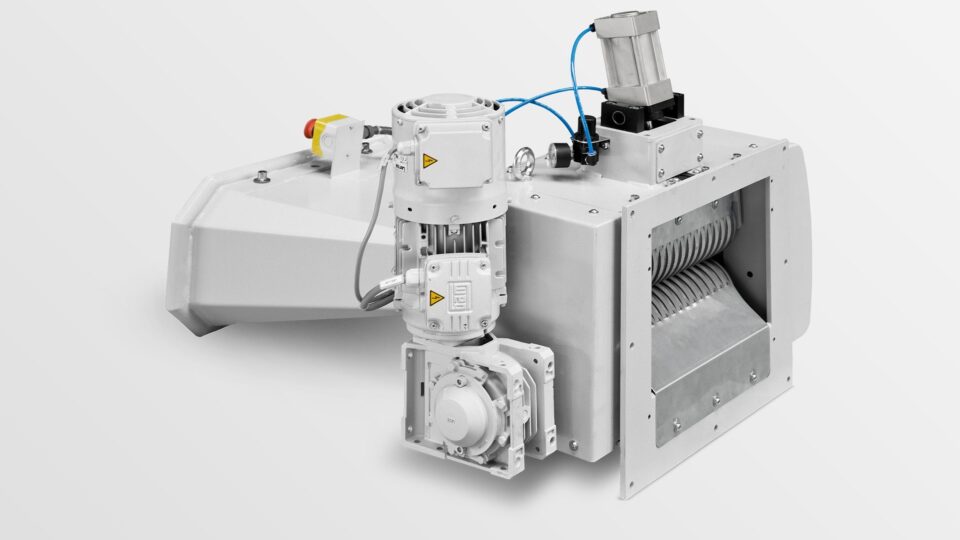
Roll feeder
Roll Feeder
With variable feed speed, roll scrap is treated in a process-controlled manner. The virtually unmanned machine is fed continuously. The roll feeder can be operated at the same time with other types of feeding (e.g. conveyor belt).
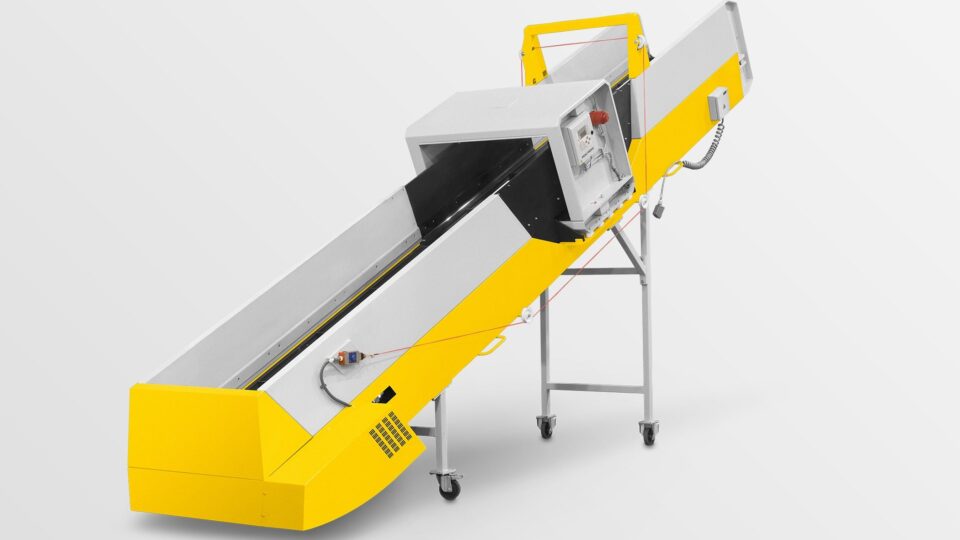
Conveyor belt
Conveyor belt
The conveyor belt transports the feed material through a metal detector into the feed hopper. The belt is stopped automatically, if metallic matter is detected in order to remove it.
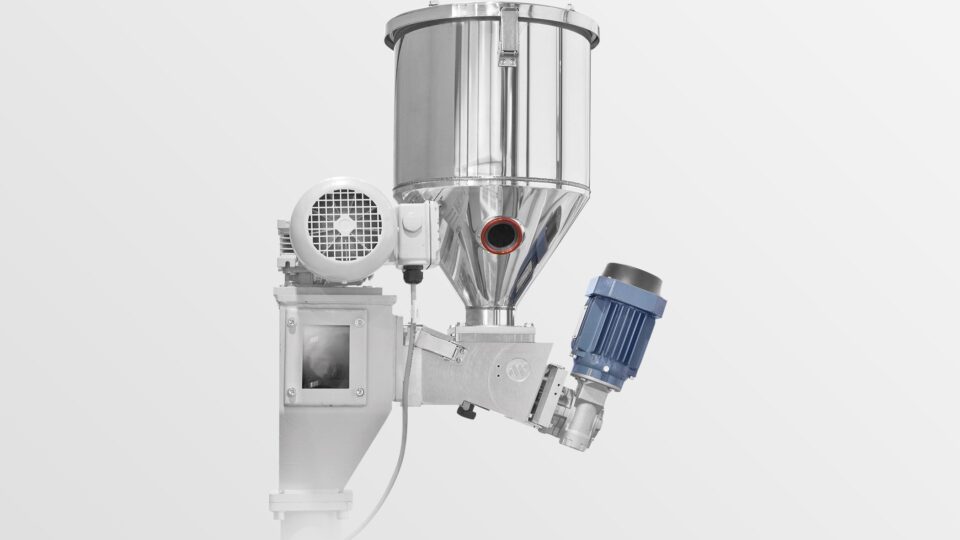
Dosing unit
Dosing unit
Additives such as color pigments, CaCo3, compatibilizers can be added to the material flow in a process-controlled manner. Dosing systems for pellet and/or powdered additives are available.
Degassing
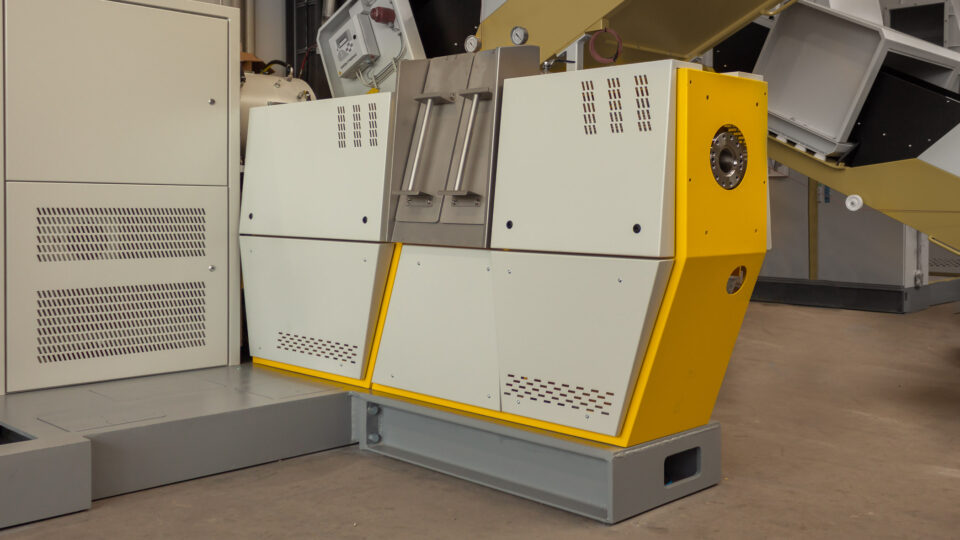
Single venting
Single venting
Designed for light printing and low humidity. The vacuum degassing system includes a vacuum pump and is connected to two venting ports on the extruder.
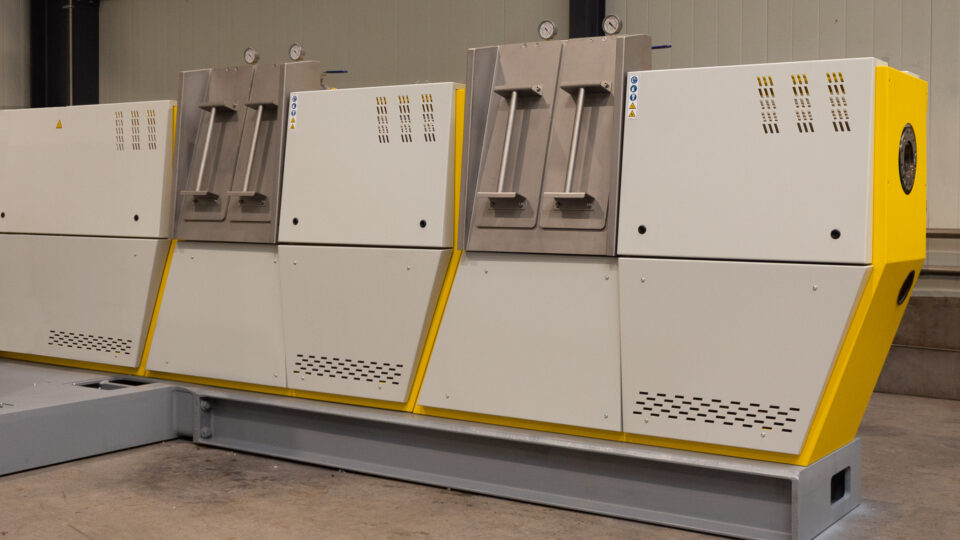
Double venting
Double venting
Designed for plastics printed, for example, on all surfaces and/or moist plastics. The simple venting unit can be supplemented by another modular unit with two venting openings and an additional vacuum pump.
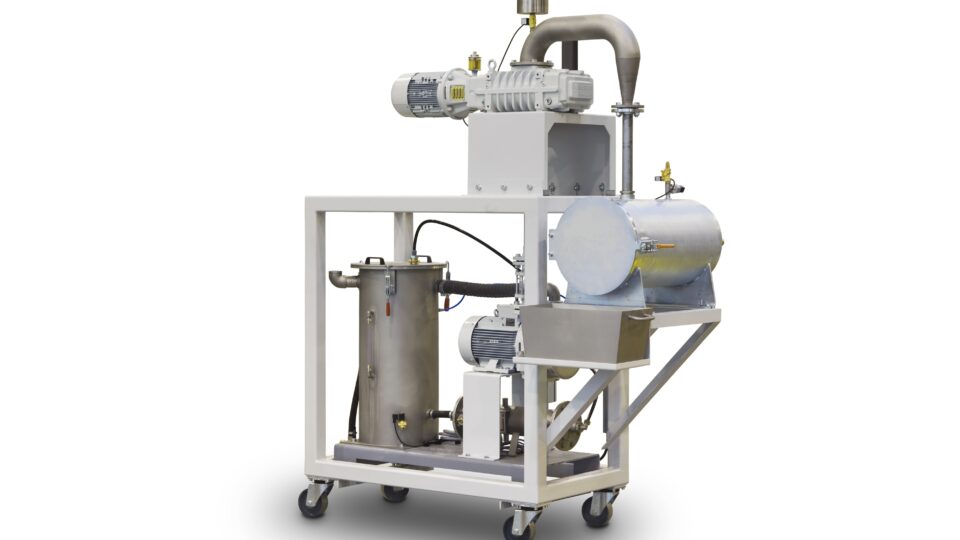
Heavy duty vacuum pump
High-performance vacuum
In addition to the modular venting unit, a combination of water ring pump and high-performance vacuum pump runs in order to increase the vacuum performance (e.g. PET processing).
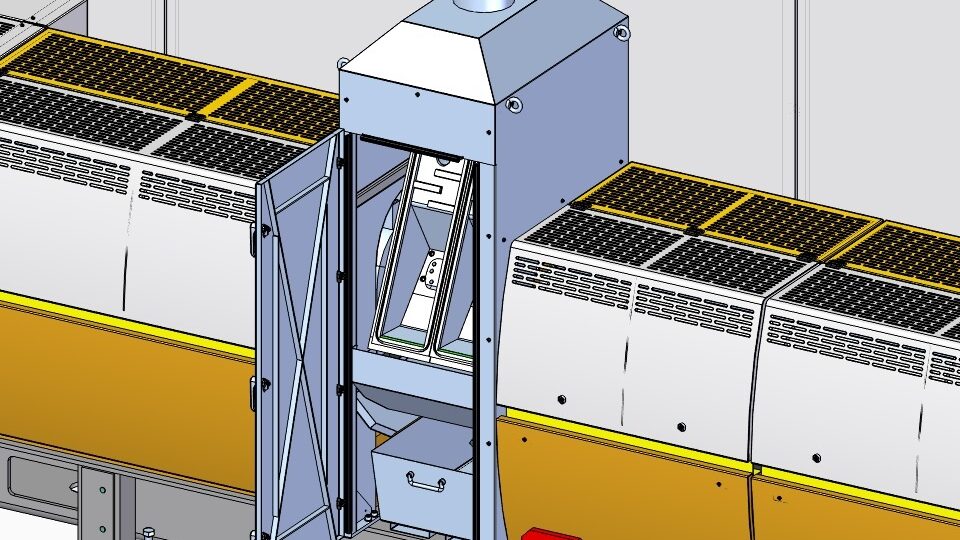
Combined venting
Combined venting
For damp materials, e.g. after washing, combined venting unit is used, which consists of an atmospheric and vacuum degassing unit.
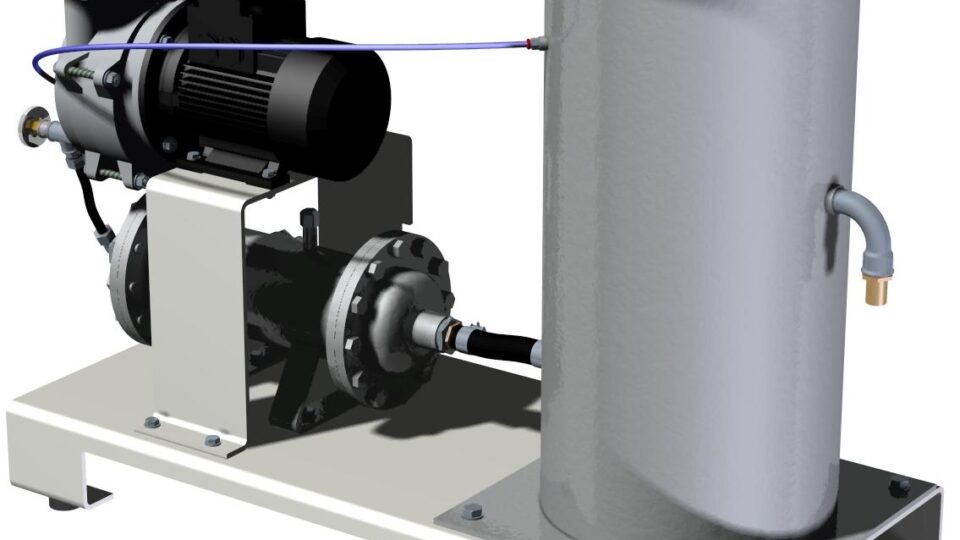
Vacuum pump with closed water circuit
Vacuum pump with closed water circuit
Each venting combination can be equipped with a closed water circuit. The fresh water consumption at the vacuum pump is thereby reduced significantly.
Pelletization
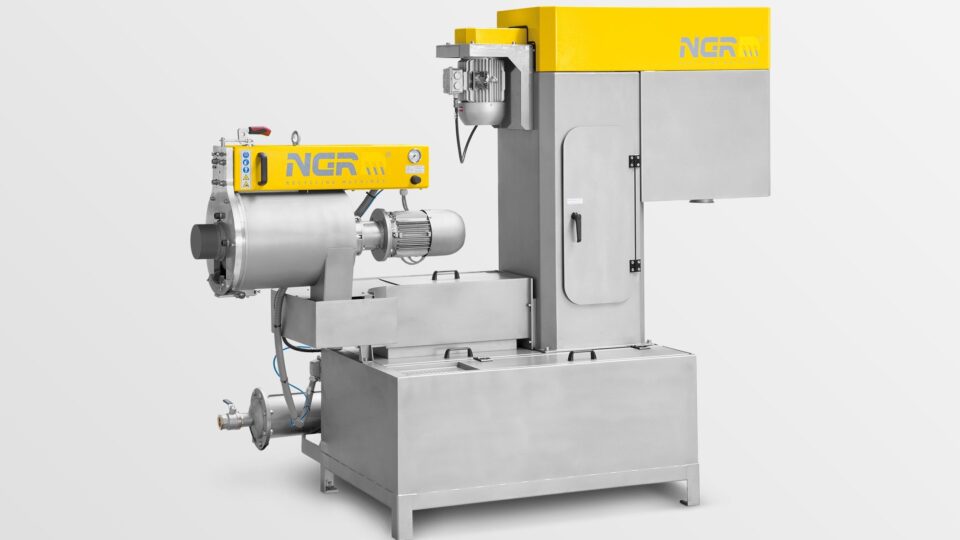
HD pelletizer
Hot-die Waterring Pelletizer (HD)
For thermoplastics with a higher viscosity. The melt exits through the wear-resistant die plate, and is knocked off by the pelletizer blades. The pellets cooled in the water ring are flushed out, dried in the centrifuge and discharged. By adjusting the blade pressure, pelletizer blades provide a long service life; replacement is quick and easy.
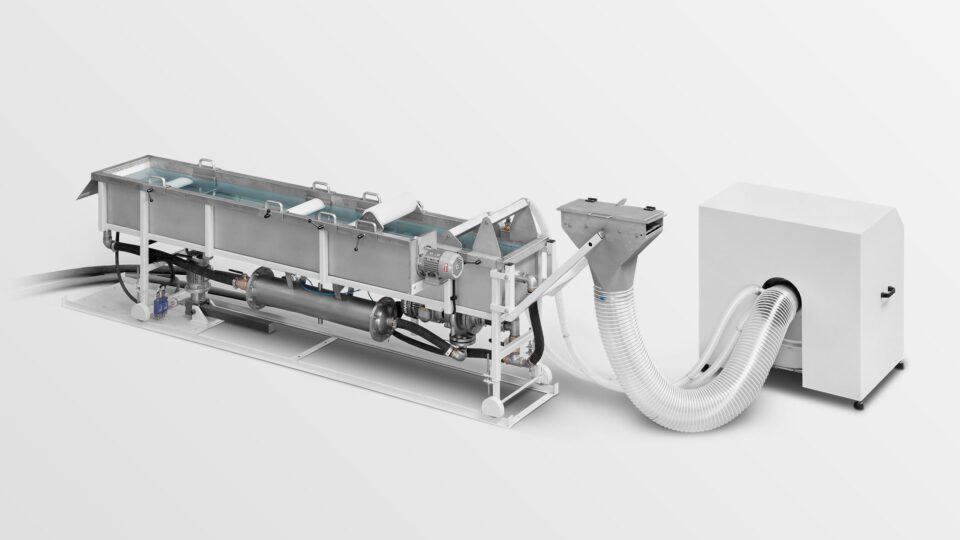
Strand pelletizer
Strand pelletizer (SP)
For low-viscosity melts. The melt emerges from strand nozzles, is cooled in a water bath, dried by means of a fan and cut to the desired length in the pelletizer. The result is cylindrical, dust-free pellets with excellent mixing properties.
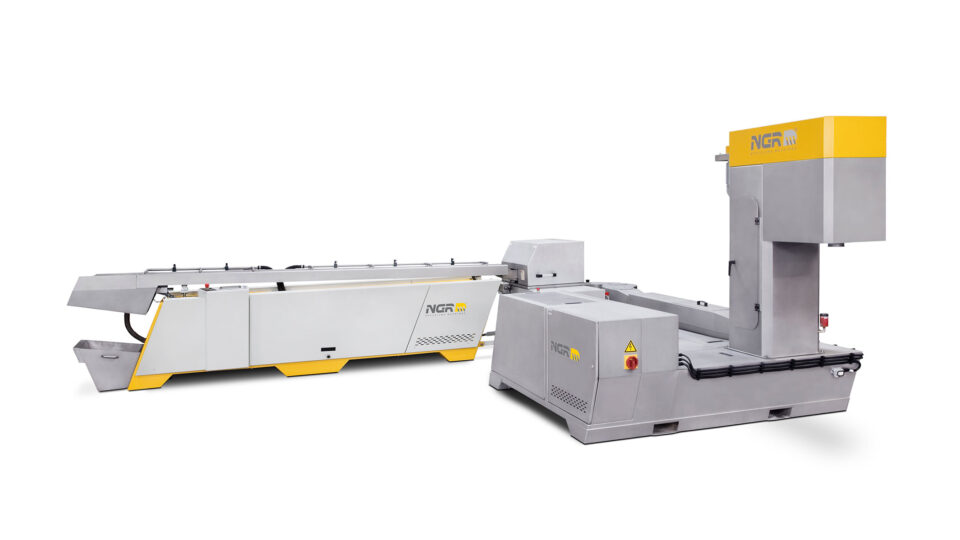
Automatic strand pelletizer
Automatic strand pelletizer (A-SP)
In addition to the benefits of the SP, the A-SP option offers the added convenience of fully automated start-up. The strands are transported automatically by a water slide to the pelletizer, and the pellets are dried in a centrifuge.
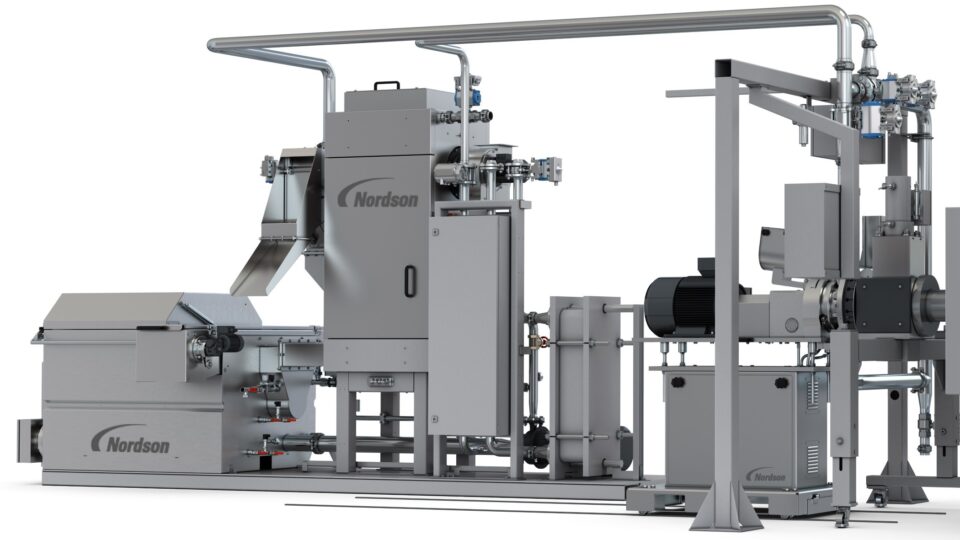
Under Water Pelletizer
Underwater pelletizer (UWP)
For difficult-to-process (e.g. sticky) polymers or thermoplastics with a very high melt flow index. The melt emerges from the die plate and is knocked off by the pelletizer blades. The whole process takes place under water. In the centrifuge, the pellets are separated from the process water and dried.
Filter
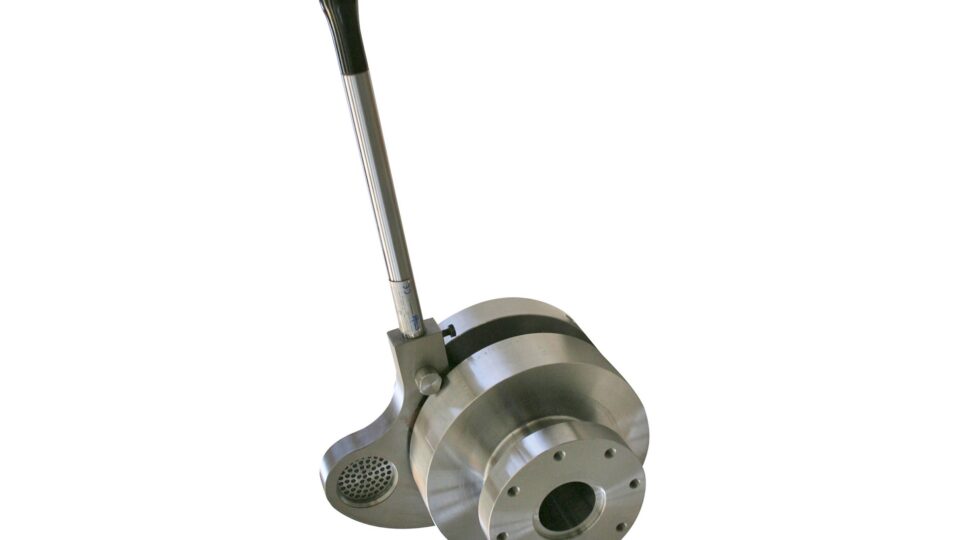
Manual screen changer
Manual screen changer
For clean, in-house production waste. Using the manual lever, two screens can be swung out alternately to allow for cleaning of the melt stream. The process is discontinuous, because the machine has to be switched off to change the screen.
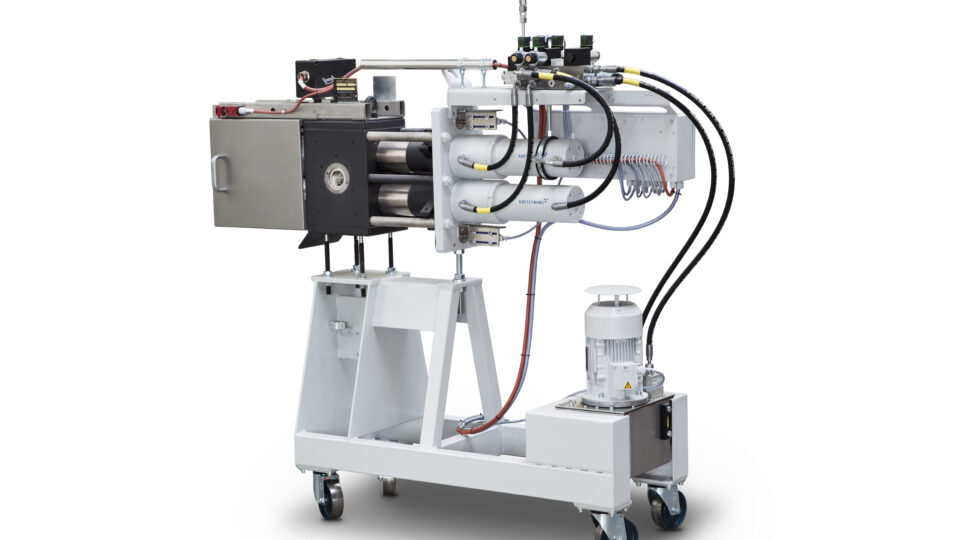
Double piston screen changer
Double-piston screen changer
For light impurities. The hydraulically operated double-piston screen changer allows continuous filtration of the melt. This allows a screen change without process shutdown.

Backflush screen changer
Back-flush screen changer
For heavily contaminated materials. The hydraulically operated double-piston screen changer filters the melt in a process-controlled and continuous manner. The integrated backwash device automatically cleans the screens. The number of back-flushes and the related service life of the screens depend on the degree of contamination of the material.

4K Backflush screen changer
4K back-flush filtration
For heavily contaminated materials. In contrast to the standard backflush screen changer with 2 screen cavities, this system is equipped with 4 screen cavities. The double filtration surface with the same frame size results in a longer filter life.
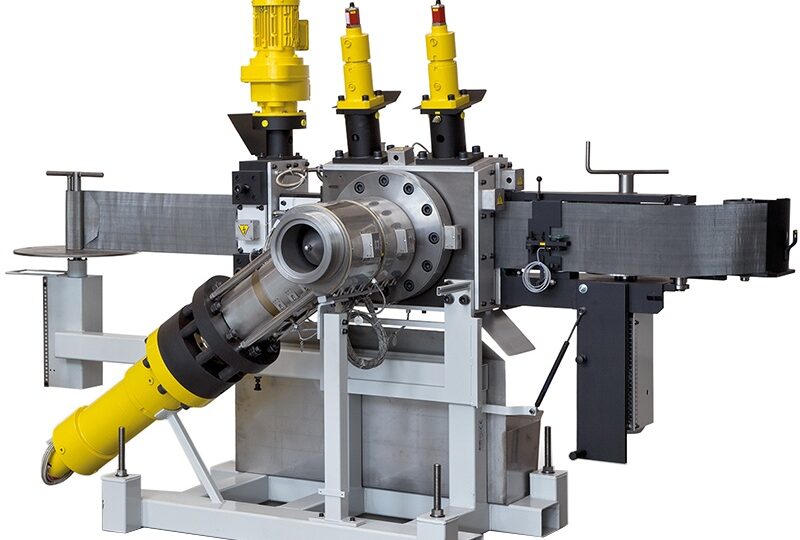
Automatic band melt filter
Band melt filter
For high contamination at high throughput rates. With the lowest melt losses and low filter costs, fully automatic operation ensures excellent filtration results. It is used particularly for post-consumer plastics.
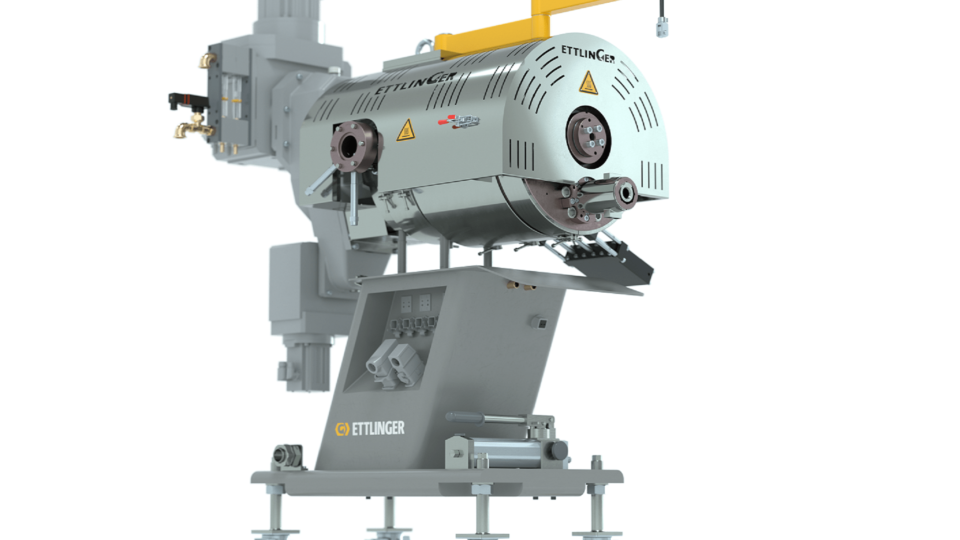
High-performance melt filter
High-performance melt filter
The continuous melt filters in the ERF series are suitable for a wide range of moderate and highly contaminated polymers and provides a pressure constant operation, long screen lifes, very low melt losses and a compact design. By the permanently rotating filter drum foreign particles are being constantly and effectively removed, depending on the application ERF melt filters enables throughputs from 150 to 10,000 kg/h.
Peripherals
Test equipment
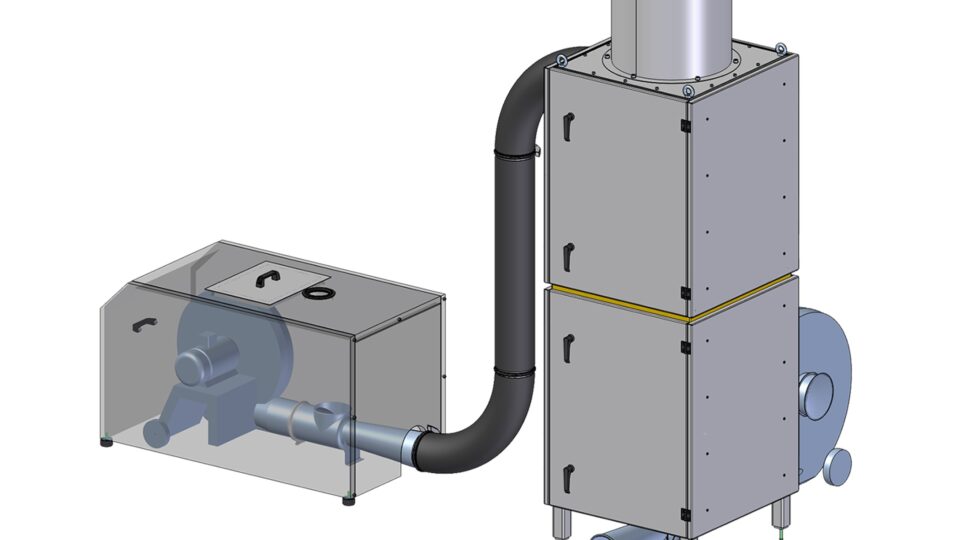
Flow scale
Flow scale
The throughput scale is integrated in the machine control system and displays the current production output in kg/h (lbs/hr). The data can be logged in a BDE system.
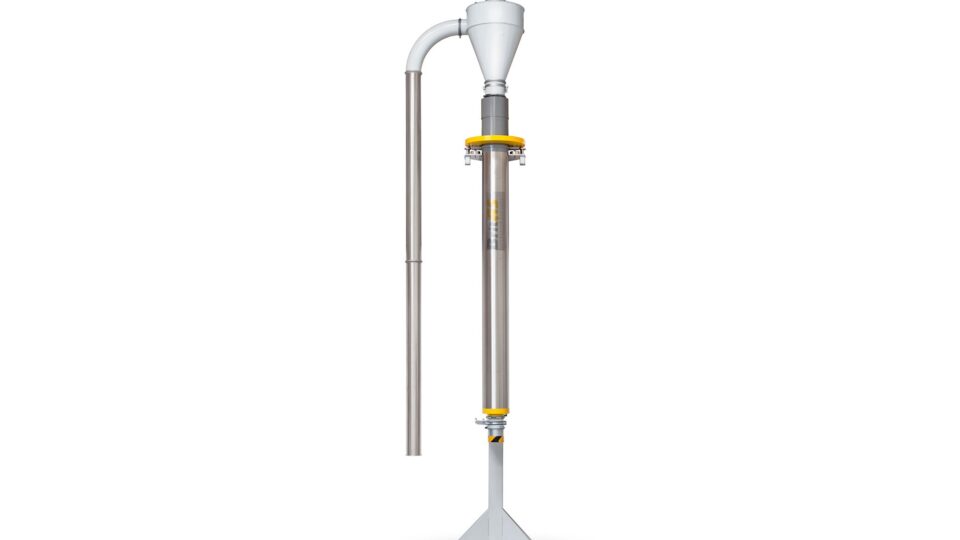
Gas control unit
Gas control unit
This unit provides quality control by continuously measuring pellet density. Based on preset parameters, the unit determines whether to switch the gates to the second choice or to scrap when this value falls below a setpoint. Monitoring is inline and integrated continuously in the production process.
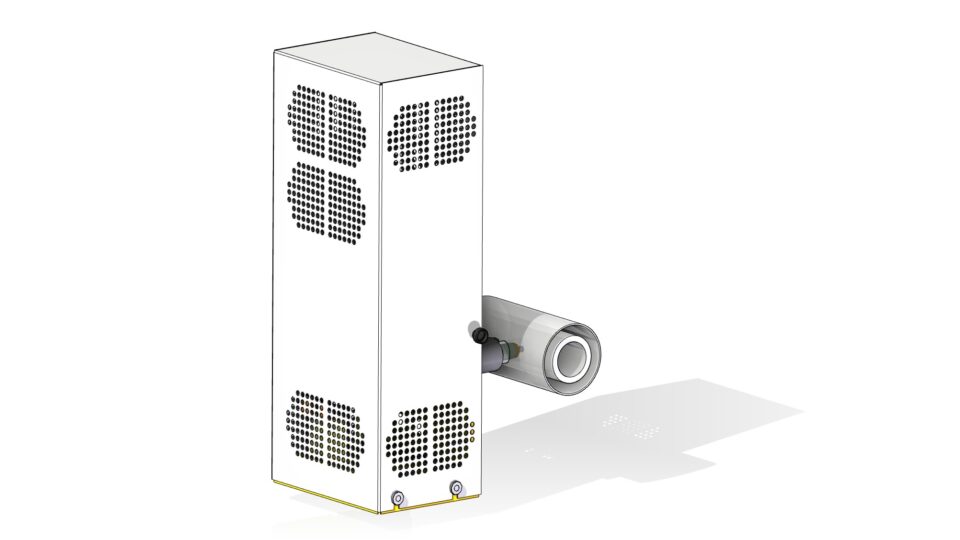
Online viskosimeter
Online Viscometer
For continuous melt viscosity measurement. Melt is taken from the production extruder, the viscosity is measured, and then the melt is returned to the extruder.
Based on the differential pressure across the capillary, the viscosity of the material (IV value, MVR) is determined by means of a stored recipe.
Material samples
Gallery
Images
Solid engineering, high-quality materials and precise execution ensure a long service life for equipment.
maintenance-friendly access to moveable parts allows you to quickly change material, efficiently disassemble and assemble wear and tear parts, and minimizes downtime.
The solidly-constructed, low-speed shredder combined with hydraulic-driven pusher also provides efficient shredding of bulky plastic scrap.
Testimonials
NGR machines are very good and very strong machines to work with. The old baby is still going strong, even-though it´s already almost 20 years old. NGR´s service technicians are very experienced and knowledgeable during the few occasions we needed them. Spares are easily available even in South Africa.
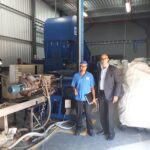
Rishi Nunkumar, Waste General Officer
Spunchem, South Africa
Over the past few years our NGR machine has been invaluable in providing us a sustainable solution in converting our waste into quality recycled materials thereby saving us money.
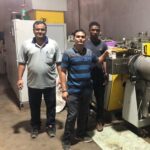
Arun R. Gwalani, CEO
Mercury Mills, Nigeria
The function of our NGR machine is very good and very easy for the operator. Tackling of the very few little problems and the maintenance are very easy, because the machine manual is very detailed and shows all maintenance positions and their timing schedule. The communication with NGR is excellent and their reaction, instant!

Konstantinos Kanellos, Co-owner
Kios Plast, Greece
Success Stories S:GRAN
Support
Our all-round service – satisfaction included
Excellent technology calls for excellent service. Our 100% commitment to flawless service ensures maximal cost efficiency and minimal downtime.
Our services
- Service hubs for the fastest possible processing of all maintenance and repair work
- Spare parts centers for flexible responses to strong markets
- High spare parts availability thanks to particularly high stock levels in Europe and North America
- Worldwide extruder screw production for short-term production or repairs
- Starter and spare parts packages for every new machine
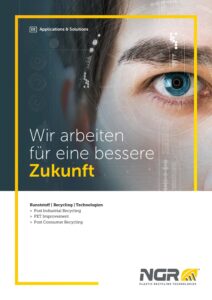
NGR Applications & Solutions
[5 MB]